荐读 | 英特尔:初探 “边缘控制”
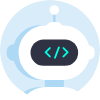
导读:本文从实例引出“边缘控制”——边缘计算在工业自动化领域的融合性应用技术,简单梳理了对相关概念的一般性理解,并给出了“云、边、端”三层参考架构和“三步走”的目标规划,介绍了基于通用计算平台的实现边缘控制的优势。举例说明了当前落地的挑战,并进行商业可行性的分析,还针对国内企业给出了一些参考建议。此外,以“英特尔工业边缘控制平台”为例,通过主要功能组件的介绍,尝试提炼出开放边缘控制系统——基于通用计算硬件、功能由软件定义——应具备的基本特征、相较传统自动化的优势和设计执行的相关任务。最后,从发展前景、实现路径和意义等方面,对边缘控制技术进行了总结。
某头部自动化公司的成都数字化工厂需要大量的印刷电路板(PCB)用于生产。为确保“零缺陷”,该厂利用自动化光学检测(AOI)系统,对PCB产品进行判别。其严格的检测规则和阈值设置,导致此AOI系统判定的“缺陷”产品,经复核实际为“假缺陷”。因此,该工厂不得不增设人工复检环节,由此带来的大量重复劳动增加了该厂生产PCB的成本。
为了解决这个问题,该厂决定引入人工智能的方法——即利用基于机器学习的检测手段来降低“假缺陷”的检出率,从而减少人工复核的劳动量。AOI检测所需的人工智能计算模型,是基于前期数据经验,在云端利用高阶算力训练完成的;在生产现场,则利用了搭载人工智能推演芯片模组的边缘计算平台进行推理应用。此种架构还可以满足制造业对“敏感数据不出厂”的安全性需求,大大降低直接将数据上传云端可能会发生泄露的风险。
依靠人工智能视觉检测,在确保PCB产品100%“零缺陷”的前提下,该方案的实施,相较此前降低了75%以上的人工复检劳动成本。
以上描述了一个利用边缘计算平台,使人工智能得以在工业自动化工厂的应用,降低生产成本提升效率的真实案例。
随着边缘计算技术的不断深入发展和广泛普及,其应用已从面向终端消费者的移动互联网应用——诸如:线上零售、游戏娱乐、视频安防、交通出行和金融服务等领域,开始渗透并主动拓展到了以传统工业自动化技术(OT技术)为主导的制造业中。在产业界实践中,边缘计算这一IT技术表现为越来越与OT技术进行联合应用的趋势;在学术理论探讨中,也相应地催生出“边缘控制”这样一个融合了“边缘计算”和“工业自动化”的新兴概念;理论研究与技术实现间相互促进,共同发展,极大地推动了各参与方就边缘计算相关技术进行持续研发投入和积极落地尝试。
本文旨在从技术简介、期望和挑战、商业考量和解决方案等几个方面,对边缘控制的相关概念和技术进行粗浅分析和初步探讨,以期对相关讨论有一定的助益:
(1)从现实技术基础和市场实际需求两个角度综合考虑,“边缘控制”技术,能否在短期内实现大规模普及,并实现具有商业价值回报的落地应用?
(2)作为工业自动化必然的技术发展趋势,对产业链上相关各类厂家,特别是中小型企业,若规划进行边缘控制技术的相关开发和积累,那需要怎样的开发范式和工具,以助其现有自动化核心产品的升级换代?
1 技术简介
1.1 边缘计算
边缘计算技术,是在互联网的云计算服务广泛普及之后应运而生,其目的是要解决云模式下如延迟较高、网络不稳定、用户端带宽低等性能问题,为终端用户提供快速、稳定、可扩展的增强型云模式的服务——即业务处理不发生在本地,而在远端的集群数据中心上。
具体实现是在传统云计算的两层结构间,增设一个具备很强处理能力和较丰富资源、并且位置上更靠近终端用户的“边缘层”。所以,边缘计算从功能逻辑角度上可视作一个三层分布式计算架构。层与层间依靠网络通信来实现数据交互。其中,边缘层对下,通过将云的处理能力和计算资源等迁移至或缓存在靠近终端用户的计算平台上,来实现或增强原本的云服务功能;而边缘层对上,提供了上云前用户层数据的采集操作、过滤、预处理等操作。这样的模式,既强调了云端超高算力和海量资源,又突出了边缘层强算力和低时延的快速响应特性,并且明确了端设备的主要功能是实现接口,完成设备间交互和人机交互。如图1所示。
1.2 边缘控制
应用边缘计算是为了解决云计算的短板;“边缘”这一专用称谓,也是在云计算产生并经历一段时间发展之后才出现的。边缘计算层,就是在传统云计算双层结构间诞生的夹层。按出现顺序依次是最初的单层终端模式(本地模式)、双层云服务模式(分布式)、三层的边缘计算模式。从发展规律上来看,其产生过程是由新的现实需求不断催生出新的技术,而技术发展和应用也会反向促进需求发现,这样一个“自然”的迭代过程。实际产生的各种需求,可被不同的新技术方案来尝试实现,成功的落地方案也能在市场得到快速普及。这种需求与技术双向促进发展的局面,都得益于以计算机软、硬件为主要载体的信息技术(IT)和通信技术(CT),借助各种业界标准和规范的推广和实施,而正处于一个通用和专用方案并存且均蓬勃发展的开放时代。
工控领域的大部分工厂中的传统制造过程,基本都采用了封闭式的控制和管理架构;图3是工厂自动化双层简化结构示意图,此双层架构的基础是现场控制层,由工业的现场设备(如伺服电机等各种执行机构、传感器等)与控制器(如PLC、CNC等)构成的;尽管不同制造过程在具体指标要求上会有较大差异,但现场数据交互和控制过程,均有实时性和响应确定性的要求,即在现场控制层中的均是实时控制系统,仅在程度上差异;在此之上是监控和管理层,最简单的可以仅是一些数据信息电子表格,但形势松散且无标准化,管理专业的企业都会引入如SCADA、MES、ERP和PLM等专用信息管理系统中的一种或几种,将生产制造过程和管理流程进行集成化和数字化;虽然这些系统可按咨询界较流行的ISA-95金字塔架构进行层级划分,如图2所示,在本文中,按上位机的观点笼统地将其视为属于同一层的功能模块;这些专业信息管理系统,传统上一般都有专用的软件在独立的硬件平台上提供相关服务。
在图6所示架构的边缘层中,可以按功能逻辑分成两类设备;可独立实现,也可以组合在一台边缘计算硬件设备上;如在基于x86的通用平台,边缘层所要求的控制、数据和计算任务,可进行“负载整合”式应用;边缘层中的**和控制器,基础架构相同且均具有与现场设备通信的能力;控制器是突出对现场设备的实时控制,**更强调从下层设备进行数据采集类工作;若再利用统一的工业以太网进行通信,这两类设备的数量和与现场设备的连接就可以做到按需而定;并且在云端管理支撑下,利用容器化技术,有望做到边缘设备间的在线热备、冗余切换和不停机升级等灵活和健壮部署的实现。
此外,随着计算机技术发展的持续进步,特别是CPU等硬件处理能力的突飞猛进;借助平台虚拟化等资源复用和隔离技术,促使多任务整合能力、稳定性和可靠性不断增强。现在诸如MES、ERP、PLM等传统制造业信息管理系统,已可在一台本地服务器或本地数据中心上,亦或通过互联网(Internet)在云(远端数据中心)上实现,即在工控领域呈现出了所谓“软件定义”——在通用计算平台(通用硬件、通用操作系统和中间件)上通过软件编程的方式实现专用功能——的发展趋势,目的是借此方式大大提高计算平台的利用率和功能实现的灵活性,利用软件充分发挥当前高性价比,特别是高性能的硬件的真实计算潜力。
2 期望与挑战
如上所述,“边缘控制”是边缘计算对工业自动化技术的一次融合。参照业界现况,推断当前对其主要期待可能是在已非常成熟的自动化产业中,通过对完全打通的数据链路和对数据进行充分地挖掘(多元数据采集、处理、分析和利用),来协助基于数据驱动和“人工智能”的应用落地,如预测性维护、数字孪生、基于视觉等新测量手段的质检品控等。
这些应用的共同特征是在软件中所采用的(数学)模型规模非常大,内部关系特别复杂;目前,对模型结构和参数,尚缺少统一的理论上合理且对现实操作有指导意义的解释;对模型判别的准确性要求高(特别是数字孪生)、用于训练用的工业数据的完整性难度大、投入人力和物力成本高,而目标达成后可产生可观的收益。因此,这些对“边缘控制”相对较强需求方向,大多数集中在大型制造企业的高利润或高端产品的制造过程中。
以“数字孪生”为例,其目的是从数字信息世界的孪生体模型中,获得对物理世界的真实设备的全生命周期的准确预测,从而给生产、维护和改进提供更加精确的决策依据。在工业场景中,需要对现场设备的运行状态,进行全过程实时监控、数据采集、高效的处理,以便提供给部署在集群上的数字孪生体模型进行仿真推理、模型修正和分析预测之用。
面临的主要挑战,一是当前技术是否可实现期待中完美匹配的仿真模型;二是单从数据采集而言,需要用到支持相同通信协议或支持转换互通的边缘控制设备,来实现现场数据实时采集,同级和上传交互,从而提供生产商对硬件配置的灵活性;换个角度看,这也避免了“边缘控制”领域出现封闭的技术和市场垄断,减小不必要高成本投入。
综上,依托“边缘控制”实现的制造业转型和新技术革命,会呈现出“期望高回报、技术高难度、持续高投入”的特点;目前技术方案和路线很多,但确定路径尚在探索之中,这也是另一个现存的挑战。
3 商业考量
在现实的商业世界中,对于着眼于当下生产需求、更考虑投入产出比和利润的内资中小型制造企业而言,应用已有的可靠自动化技术“活下去”才更重要,但同时又在成本可接受的范围内进行未雨绸缪的规划和准备。而对于内资自动化大厂,虽有较雄厚实力,可进行“未来概念”领域的布局,但在技术路线和相关资源的选择上也应借鉴现有的成功案例和经验,不可也应该不会是“大干快上”的局面,建议在权衡投入产出比,逐步看到技术和利润回报的前提下,多利用和借鉴可供利用的资源(特别是现有质量高的开源资源和可靠的低成本授权的资源),进行小步稳走的发展模式。
4 解决方案
首先介绍由英特尔工业团队发布的边缘控制解决方案,依次概述其设计理念、模块组件和功能特点;然后以这套方案为参照,分析“边缘控制”的软、硬件需求和关键特征;再将开放自动化与传统自动化,进行比较;最后尝试提供一些建议,以进行技术路线决策时进行参考。
参照ECI,对边缘控制解决方案应具备的特征,提出如下几点思考:
· 多种功能集中在同一控制器上实现,如:运动和逻辑控制、人机交互(HMI)和基于机器视觉及其它传感器的感知功能;过去需多台设备共同协作,现在则仅需一台具有强处理能力的边缘控制器;
· 自动化设备间的联合与协同控制,如:一条多机加工位的FMS(柔性)产线,物流和机床上下料控制,视觉检测和功能安全等;
· 南向通信:用各种工业以太网和现场总线方案,连接工业现场的执行器和传感器;
· 北向通信:通过工业以太网,连接车间和工厂信息管理系统,也包含控制器间的通信;
· 同级通信:控制器间互为上下位机,从“互联互通”向“互操与互换”演进。
· 数据接口:边缘侧提供数据接口,采集工业4.0和工业物联网场景下各种泛在数据;
· 感知能力:主要是基于机器视觉检测、测量;联合其它传感器,建立和实现一定程度上的类人感知功能;增强实时获取工业信息的能力;
· 数据能力:利用机器学习、深度神经网络等AI工具,并结合传统的工艺经验模型,使机器在获取足够感知信息基础上,具备自主进行判读和处理的能力。
· 云端:处理能力强,计算资源丰富;任务负载迁移灵活,资源可在线升级和扩容;
· 边缘:低延时、网络稳定、避免带宽不足;数据不出本地,便于敏感数据的保护。
5 结论
本文通过梳理对相关概念的理解,研判产业现状和落地挑战,再综合考量内资公司特别是中小型自动化企业进行决策的商业因素,并对边缘控制方案所应具备特征等进行介绍后,总结出如下认知要点供参考:
(1)相较于由大量、普遍的需求而推动诞生的“边缘计算”技术,“边缘控制”更像是在发展趋势(主要动力)和少量高端技术需求共同推动下产生的。换言之,“边缘计算”更像是普遍需求推动的技术发展,而“边缘控制”则更像是技术发展带动的需求发现。
(2)在硬件部署、改造升级方面,工业自动化从“封闭式控制”转到“边缘控制”具备硬件基础优势,可以通过添加/升级/改造“管理层”或“控制器层”,更快、更优地实现“端、边、云”三层结构。
(3)“边缘控制”可通过仅在“边缘端”应用模型、处理和存储数据,实现生产线能力优化的同时保护客户的敏感数据。
(4)虽然“边缘控制”实现了技术发展,但受限于使用场景、现实需求的必要性、投入产出比、自动化市场的产业结构(企业利润率及竞争激烈程度)等因素,对该技术的实际使用需求量还是较少,“边缘控制”仍主要存在于产业的“未来布局”概念中,短期内得到普及性应用的基础较为薄弱,需要推动和持续发展。
(5)对IT、CT和OT融合的持续研究和投入具有长久而深远意义。在更低成本、更高效率且能实现相同功能的新技术出现前,“边缘控制”仍然是最有可能成为:在未来的某个时刻,爆发出普及性应用需求的某些领域中,既存的技术扩展和补充,或某些普及技术的基础原型。
文章转载自:控制网